Industry 4.0 is About Creating Extended Value
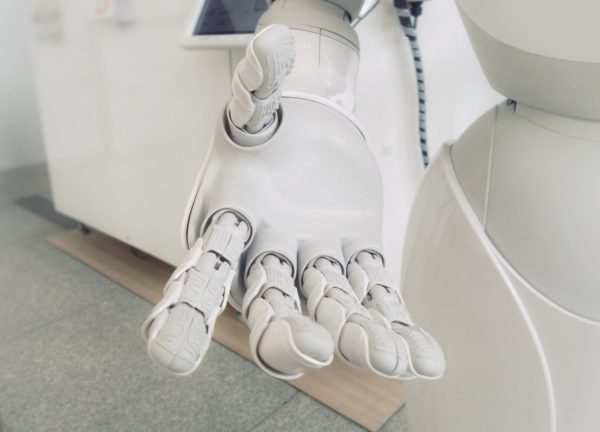
Often when a company is looking to modernize or update their systems to join the Industry 4.0 revolution, they are bombarded by sales agents looking to sell their product of the day. What should a company look for? How do you cut through the hype to determine the tangible and intangible benefits?
When evaluating automation systems, direct value can easily be measured. For example, if a new press machine will improve efficiency by 20% and decrease labour by 10%, then it is relatively easy to determine the value of that machine to the organization. If the total value of a system is much greater than the total cost, then the system should be considered for implementation.
Extended value also examines the longer term and often intangible benefits for a solution. For example, a new machine might also reduce the number of failed parts, have lower maintenance or operational costs, or may reduce employee strain. These benefits are difficult to quantify up front, however an experienced and forward-thinking manager often recognizes these characteristics as valuable and can lead a company to invest in a new system.
Adding computer intelligence to the manufacturing process is not a new idea. However, the rapid growth of computing technology and capability makes it difficult for even the most experienced technology professional to keep up. As new technology capabilities are introduced, what wasn’t possible last year may now be possible this year. It is a full-time job to constantly learn about new technology and examine how this technology can be implemented in a meaningful way within an organization. This struggle is not unique to manufacturing, all industry sectors find themselves in a pattern of trying to relearn and reinvent themselves as part of a continuous improvement process.
This is the very reason why some companies may be slow to adapt to industry 4.0 ideas, as the intangible benefits can often be difficult to quantify, manufacturing specialists are not computing experts, and computing experts are not manufacturing experts. It’s only through the meaningful exchange of ideas, identification of pressure points and collaboration by individuals with diverse backgrounds can innovation flourish. As it has been shown that the rate innovation is directly proportional the rate of communication exchange.
The lack of understanding of both advanced manufacturing and computing technology can act as a barrier to adoption. This becomes very problematic when a company is looking to evaluate the best solution for their exact business. Industry 4.0 is a very broad term that means different things to different people and it is far from a one size fits all solution.
Automation versus intelligence
When automating systems, the goal is to create better products, more reliability, cheaper, faster or more efficiently. When we talk about intelligence in a manufacturing environment, the conversation becomes more about knowledge and insight, for example “Why are parts failing?” “How can I produce just in time parts?” and “How can I make a better product?”
Simply installing sensors that measure or count parts moving along an assembly line provides great information and metrics around the overall all efficiency of an operation. You can measure the impact of speeding up a process as it correlates to the number of failed parts to determine optimum production times.
Extending beyond Automation into Intelligence
Paper-based maintenance logs can easily be overlooked, are susceptible to data transposition errors or may be misread or misinterpreted. By implementing a smart solution to monitor logs, the system not only automates this process, but can also intelligently monitor system health against an established criteria. This can reduce downtime and may even be able to recommend additional proactive steps beyond the manufacturer’s recommendations by considering the environment, raw materials being used, and specific type of tool heads being used.
When you begin to consider external environmental factors such as raw materials through pattern recognition consistency, machine wear, debris, consistent line pressure, room temperature, humidity and far into their shift the operator may be, do you start to gain knowledge through pattern recognition.
The analysis of failed parts is a critical component to help identify the root cause of issues. An AI-based system could be developed to generate a holistic view of many factors, and over time, help identify the root causes.
Industry 4.0 is not a one size fits all concept; what it means, how it can be used, and where it should be used varies from business to business.
Industry 4.0 is an ideology that runs hand in hand as part of continuous improvement plan, that when properly implemented can produce untold amounts of extended value to an organization.